PCB焊盤設計工藝的相關參數
發(fā)布時間:2023-08-09作者:admin點擊:810
1. 目的
規(guī)范產品的PCB焊盤設計工藝,規(guī)定PCB焊盤設計工藝的相關參數,使得PCB 的設計滿足可生產性、可測試性、安規(guī)、EMC、EMI 等的技術規(guī)范要求,在產品設計過程中構建產品的工藝、技術、質量、成本優(yōu)勢。
2. 適用范圍
本規(guī)范適用于家電類電子產品的PCB 工藝設計,運用于但不限于PCB 的設計、PCB 批產工藝審查、單板工藝審查等活動。
本規(guī)范之前的相關標準、規(guī)范的內容如與本規(guī)范的規(guī)定相抵觸的,以本規(guī)范為準
3.引用/參考標準或資料
TS—S0902010001 <<信息技術設備PCB 安規(guī)設計規(guī)范>>
TS—SOE0199001 <<電子設備的強迫風冷熱設計規(guī)范>>
TS—SOE0199002 <<電子設備的自然冷卻熱設計規(guī)范>>
IEC60194 <<印制板設計、制造與組裝術語與定義>> (Printed Circuit Board design
manufacture and assembly-terms and definitions)
IPC—A—600F <<印制板的驗收條件>> (Acceptably of printed board)
IEC60950
4.規(guī)范內容
4.1焊盤的定義
通孔焊盤的外層形狀通常為圓形、方形或橢圓形。具體尺寸定義詳述如下,名詞定義如圖所示。
1) 孔徑尺寸:
若實物管腳為圓形:孔徑尺寸(直徑)=實際管腳直徑+0.20∽0.30mm(8.0∽12.0MIL)左右;
若實物管腳為方形或矩形:孔徑尺寸(直徑)=實際管腳對角線的尺寸+0.10∽0.20mm(4.0∽8.0MIL)左右。
2) 焊盤尺寸:
常規(guī)焊盤尺寸=孔徑尺寸(直徑)+0.50mm(20.0 MIL)左右。
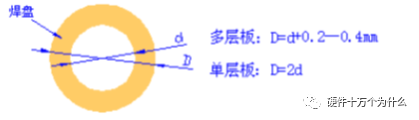
4.2 焊盤相關規(guī)范
4.2.1所有焊盤單邊最小不小于0.25mm,整個焊盤直徑最大不大于元件孔徑的3倍。
一般情況下,通孔元件采用圓型焊盤,焊盤直徑大小為插孔孔徑的1.8倍以上;單面板焊盤直徑不小于2mm;雙面板焊盤尺寸與通孔直徑最佳比為2.5,對于能用于自動插件機的元件,其雙面板的焊盤為其標準孔徑+0.5---+0.6mm
4.2.2 應盡量保證兩個焊盤邊緣的距離大于0.4mm,與過波峰方向垂直的一排焊盤應保證兩個焊盤邊緣的距離大于0.5mm(此時這排焊盤可類似看成線組或者插座,兩者之間距離太近容易橋連)
在布線較密的情況下,推薦采用橢圓形與長圓形連接盤。單面板焊盤的直徑或最小寬度為1.6mm或保證單面板單邊焊環(huán)0.3,雙面板0.2;焊盤過大容易引起無必要的連焊。在布線高度密集的情況下,推薦采用圓形與長圓形焊盤。焊盤的直徑一般為1.4mm,甚至更小。
4.2.3 孔徑超過1.2mm或焊盤直徑超過3.0mm的焊盤應設計為星形或梅花焊盤
對于插件式的元器件,為避免焊接時出現銅箔斷裂現象,且單面板的連接處應用銅箔完全包覆;而雙面板最小要求應補淚滴(詳細見附后的附件---環(huán)孔控制部分);如圖:
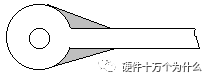
4.2.4 所有接插件等受力器件或重量大的器件的焊盤引線2mm以內其包覆銅膜寬度要求盡可能增大并且不能有空焊盤設計,保證焊盤足夠吃錫,插座受外力時不會輕易起銅皮。大型元器件(如:變壓器、直徑15.0mm以上的電解電容、大電流的插座等)加大銅箔及上錫面積如下圖;陰影部分面積最小要與焊盤面積相等?;蛟O計成為梅花形或星型焊盤。
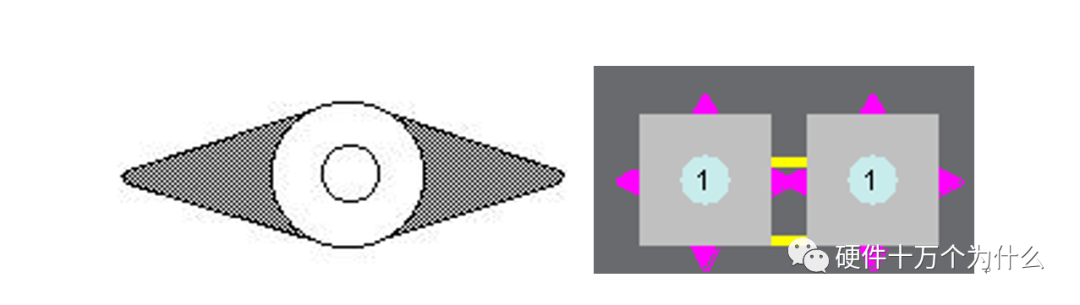
4.2.5 所有機插零件需沿彎腳方向設計為滴水焊盤,保證彎腳處焊點飽滿,臥式元件為左右腳直對內彎折,立式元件為外彎折左腳向下傾斜15°,右腳向上傾斜15°。注意保證與其周圍焊盤的邊緣間距至少大于0.4
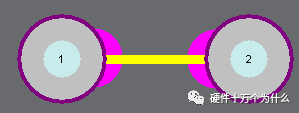
4.2.6 如果印制板上有大面積地線和電源線區(qū)(面積超過500mm2),應局部開窗口或設計為網格的填充(FILL)。如圖:
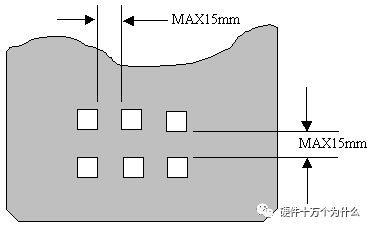
4.3 制造工藝對焊盤的要求
4.3.1貼片元器件兩端沒連接插裝元器件的必須增加測試點,測試點直徑在1.0mm~1.5mm之間為宜,以便于在線測試儀測試。測試點焊盤的邊緣至少離周圍焊盤邊緣距離0.4mm。測試焊盤的直徑在1mm以上,且必須有網絡屬性,兩個測試焊盤之間的中心距離應大于或等于2.54mm;若用過孔作為測量點,過孔外必須加焊盤,直徑在1mm(含)以上;
4.3.2有電氣連接的孔所在的位置必須加焊盤;所有的焊盤,必須有網絡屬性,沒有連接元件的網絡,網絡名不能相同;定位孔中心離測試焊盤中心的距離在3mm以上; 其他不規(guī)則形狀,但有電氣連接的槽、焊盤等,統(tǒng)一放置在機械層1(指單插片、保險管之類的開槽孔)。
4.3.3腳間距密集(引腳間距小于2.0mm)的元件腳焊盤(如:IC、搖擺插座等)如果沒有連接到手插件焊盤時必須增加測試焊盤。測試點直徑在1.2mm~1.5mm之間為宜,以便于在線測試儀測試。
4.3.4焊盤間距小于0.4mm的,須鋪白油以減少過波峰時連焊。
4.3.5點膠工藝的貼片元件的兩端及末端應設計有引錫,引錫的寬度推薦采用0.5mm的導線,長度一般取2、3mm為宜。
4.3.6單面板若有手焊元件,要開走錫槽,方向與過錫方向相反,寬度視孔的大小為0.3mm到0.8mm;如下圖:
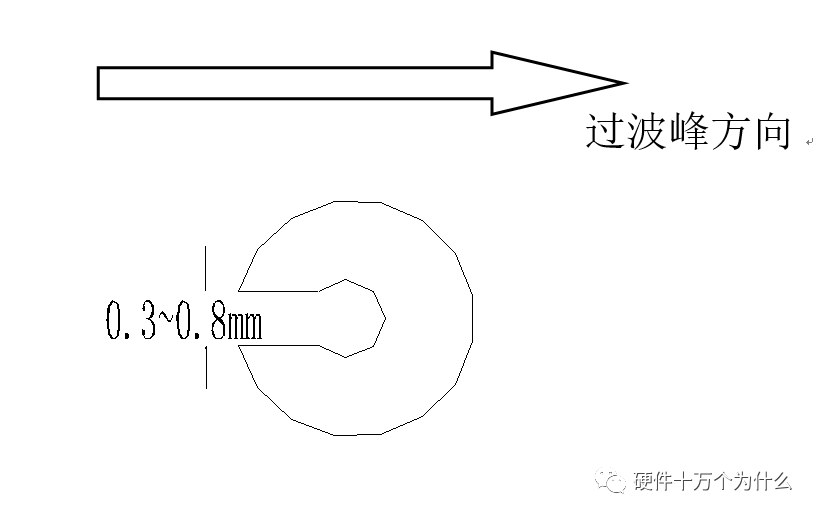
4.3.7 導電橡膠按鍵的間距與尺寸大小應與實際的導電橡膠按鍵的尺寸相符,與此相接的PCB板應設計成為金手指,并規(guī)定相應的鍍金厚度(一般要求為大于0.05um~0.015um)。
4.3.8 焊盤大小尺寸與間距要與貼片元件尺寸相匹配。
a.未做特別要求時,元件孔形狀、焊盤與元件腳形狀必須匹配,并保證焊盤相對于孔中心的對稱性(方形元件腳配方形元件孔、方形焊盤;圓形元件腳配圓形元件孔、圓形焊盤),且相鄰焊盤之間保持各自獨立,防止薄錫、拉絲;
b. 同一線路中的相鄰零件腳或不同PIN 間距的兼容器件,要有單獨的焊盤孔,特別是封裝兼容的繼電器的各兼容焊盤之間要連線,如因PCB LAYOUT無法設置單獨的焊盤孔,兩焊盤周邊必須用阻焊漆圍住
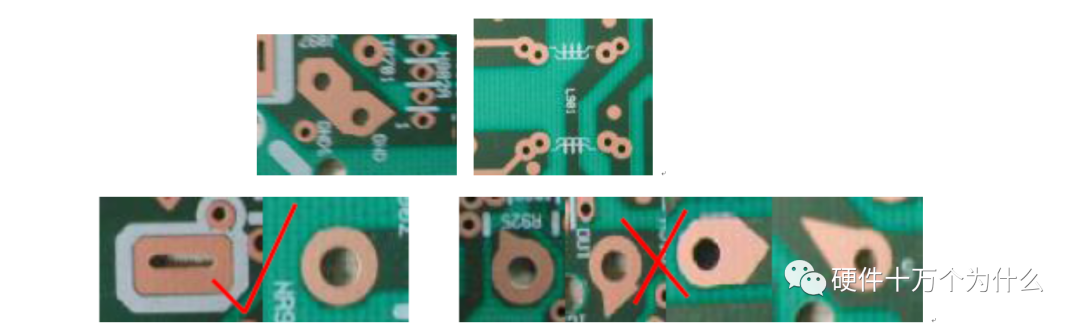
4.3.9 設計多層板時要注意,金屬外殼的元件是插件封裝時,外殼與印制板接觸的,頂層的焊盤不可開,一定要用綠油或絲印油蓋住(例如兩腳的晶振、3只腳的LED)。
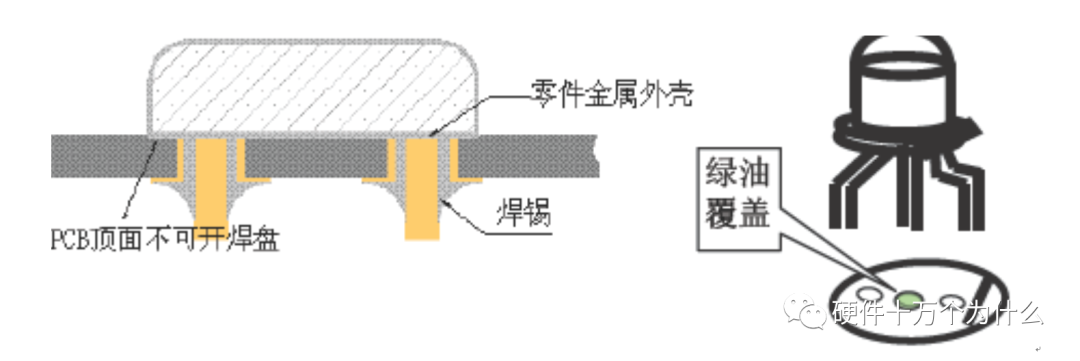
4.3.10 PCB板設計和布局時盡量減少印制板的開槽和開孔,以免影響印制板的強度。
4.3.11 貴重元器件:貴重的元器件不要放置在PCB的角、邊緣、安裝孔、開槽、拼板的切割口和拐角處,以上這些位置是印制板的高受力區(qū),容易造成焊點和元器件的開裂和裂紋。
4.3.12 較重的器件(如變壓器)不要遠離定位孔,以免影響印制板的強度和變形度。布局時,應該選擇將較重的器件放置在PCB的下方(也是最后進入波峰焊的一方)。
4.3.13 變壓器和繼電器等會輻射能量的器件要遠離放大器、單片機、晶振、復位電路等容易受干擾的器件和電路,以免影響到工作時的可靠性。
4.3.14 對于QFP 封裝的IC(需要使用波峰焊接工藝),必須45 度擺放,并且加上出錫焊盤。(如圖所示)
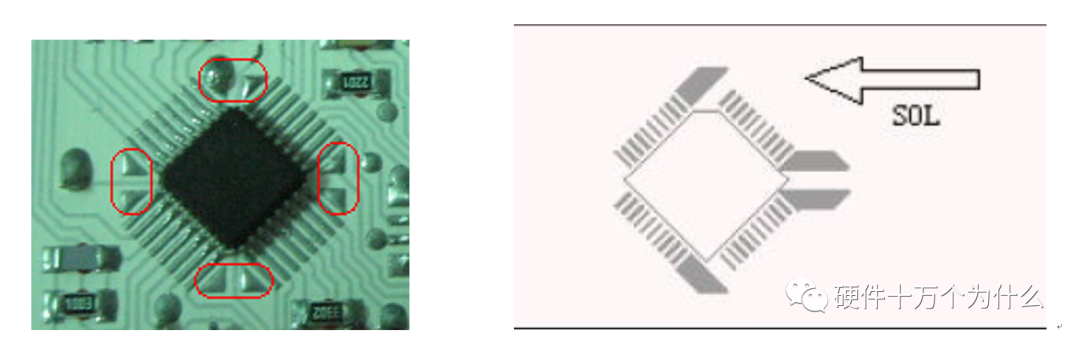
4.3.15 貼片元件過波峰焊時,對板上有插元件(如散熱片、變壓器等)的周圍和本體下方其板上不可開散熱孔, 防止PCB過波峰焊時,波峰1(擾流波)上的錫沾到上板零件或零件腳,在后工程中裝配時產生機內異物
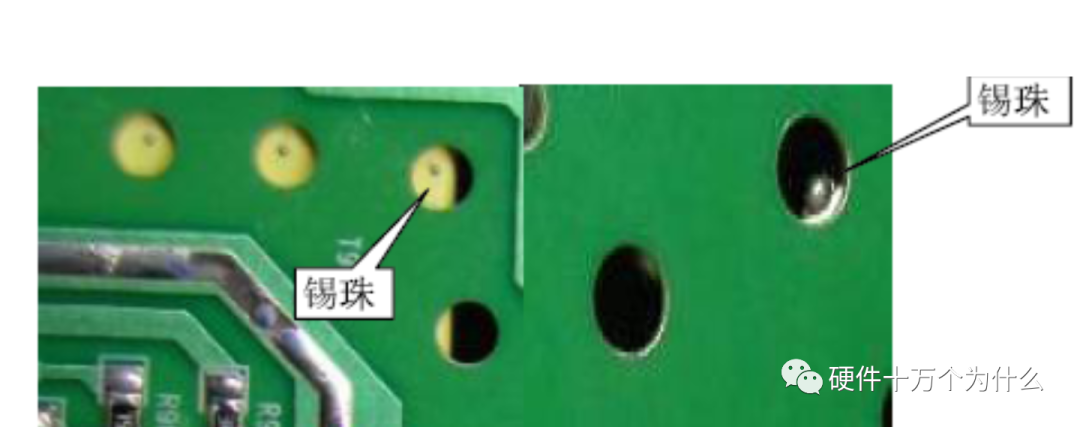
4.3.16 大面積銅箔要求用隔熱帶與焊盤相連
為了保證透錫良好,在大面積銅箔上的元件的焊盤要求用隔熱帶與焊盤相連,對于需過5A以上大電流的焊盤不能采用隔熱焊盤,如圖所示:
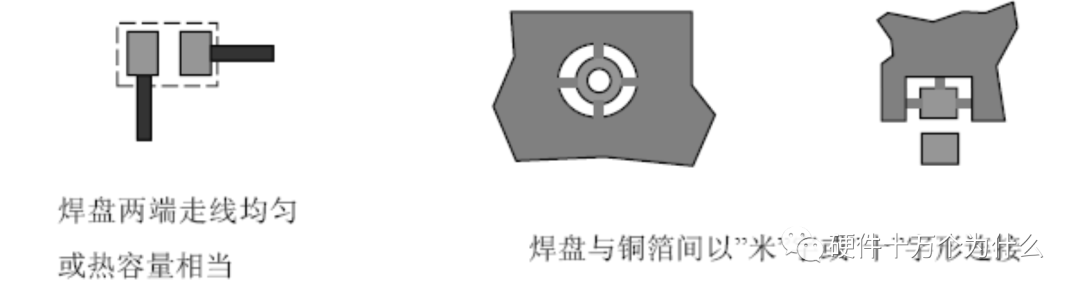
4.3.17 為了避免器件過回流焊后出現偏位、立碑現象,回流焊的0805 以及0805 以下片式元件兩端焊盤應保證散熱對稱性,焊盤與印制導線的連接部寬度不應大于0.3mm(對于不對稱焊盤),如上面圖1所示。
4.4 對器件庫選型要求
4.4.1 已有PCB 元件封裝庫的選用應確認無誤
PCB 上已有元件庫器件的選用應保證封裝與元器件實物外形輪廓、引腳間距、通孔直徑等相符合。
插裝器件管腳應與通孔公差配合良好(通孔直徑大于管腳直徑8—20mil),考慮公差可適當增加,確保透錫良好。未做特別要求時,手插零件插引腳的通孔規(guī)格如下:
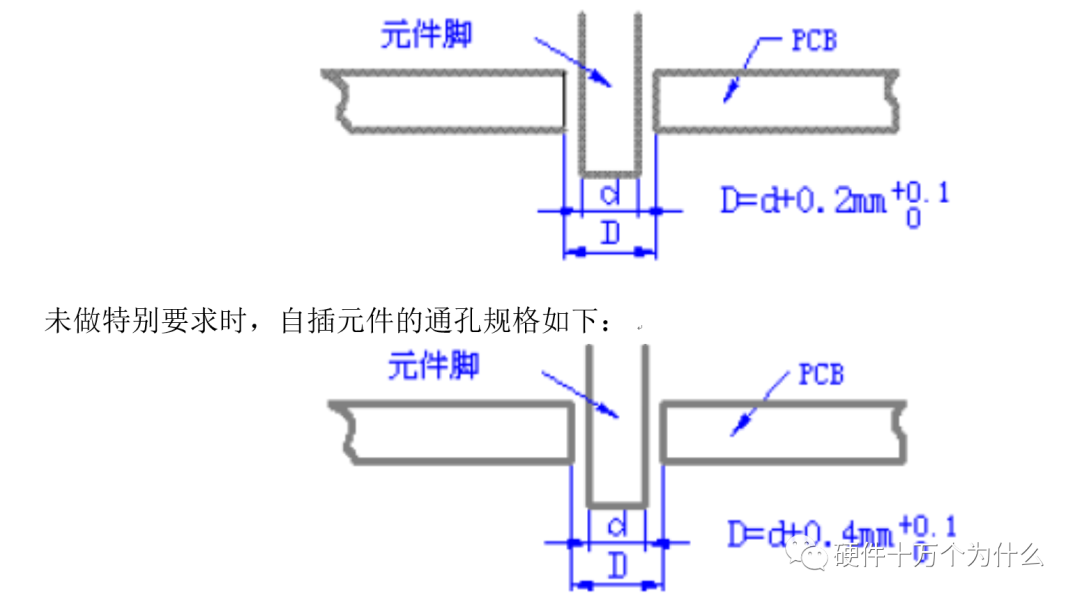
4.4.2 元件的孔徑要形成序列化,40mil 以上按5 mil 遞加,即40 mil、45 mil、50 mil、55 mil……;
40 mil 以下按4 mil 遞減,即36 mil、32 mil、28 mil、24 mil、20 mil、16 mil、12 mil、8 mil.
4.4.3 器件引腳直徑與PCB 焊盤孔徑的對應關系,以及插針焊腳與通孔回流焊的焊盤
孔徑對應關系如表1:
器件引腳直徑(D) PCB焊盤孔徑/插針通孔 回流焊焊盤孔徑
D≦1.0mm D+0.3mm/+0.15mm
1.0mm
D>2.0mm D+0.5mm/0.2mm
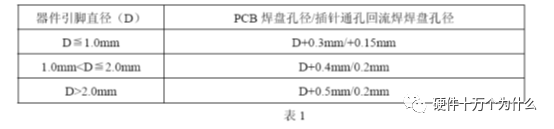
建立元件封裝庫存時應將孔徑的單位換算為英制(mil),并使孔徑滿足序列化要求。
4.4.4 焊盤圖形的設計:
4.4.4.1原則上元件焊盤設計需要遵守以下幾點
4.4.4.1.1盡量考慮焊盤的方向與流程的方向垂直
4.4.4.1.2焊盤的寬度最好等于或稍大于元件的寬度;焊盤長度稍小于焊盤寬度的寬度
4.4.4.1.3增加零件焊盤之間的間隙有利于組裝;推薦使用小的焊盤
4.4.4.1.4MT元件的焊盤上或其附近不能有通孔,否則在回流焊過程中,焊盤上的焊錫熔化后會沿著通孔流走,會產生虛焊﹐少錫﹐還可能流到板的另一面造成短路
4.4.4.1.5焊盤兩端走線均勻或熱容量相當
4.4.4.1.6焊盤尺寸大小必須對稱
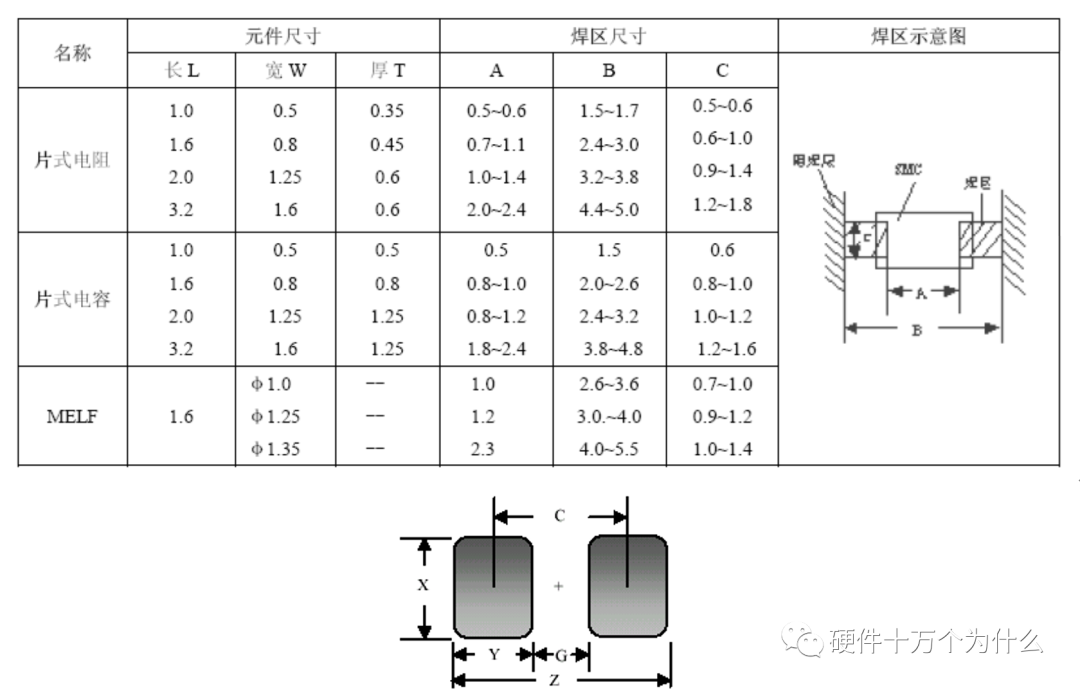
4.4.4.2片狀元器件焊盤圖形設計(見上圖):典型的片狀元器件焊盤設計尺寸如表所示??稍诟骱副P外設計相應的阻焊膜。阻焊膜的作用是防止焊接時連錫。
4.4.4.3 SOP,QFP焊盤圖形設計:SOP、QFP焊盤尺寸可參考IPC-SM-782進行設計。
對于SOP、QFP焊盤的設計標準。(如下圖表所示)
焊盤大小要根據元器件的尺寸確定,焊盤的寬度=引腳寬度+2*引腳高度,焊接效果最好;焊盤的長度見圖示L2,(L2=L+b1+b2;b1=b2=0.3mm+h;h=元件腳高)
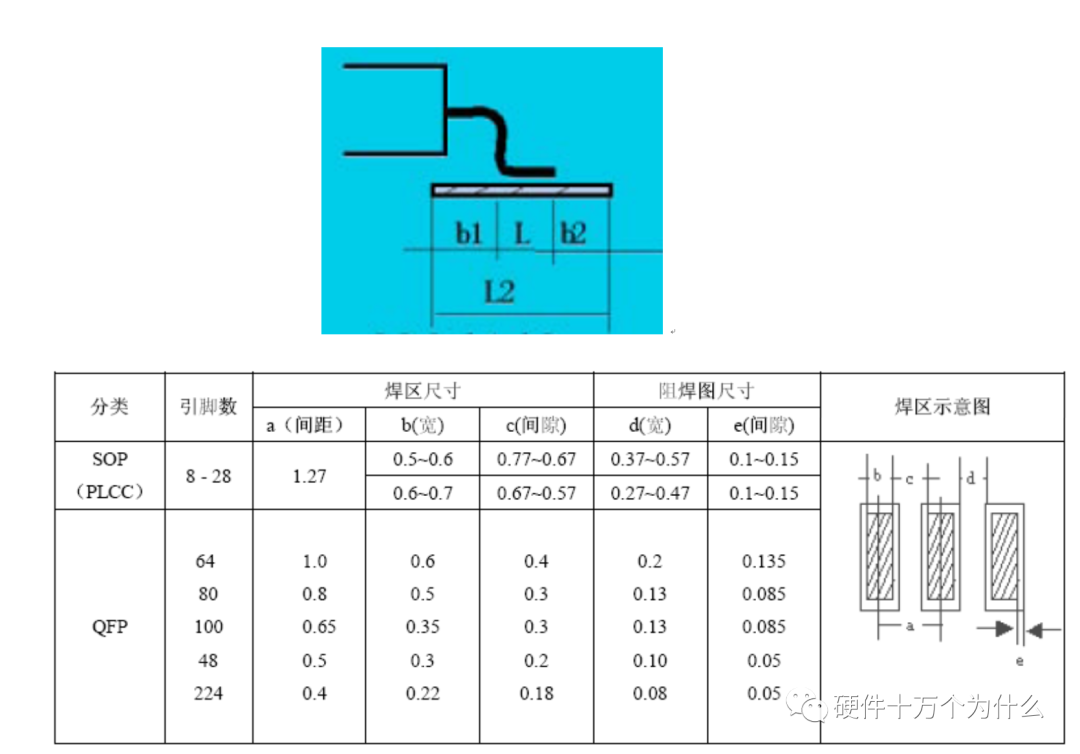
4.4.4.4未做特別要求時,通孔安裝元件焊盤的規(guī)格如下:
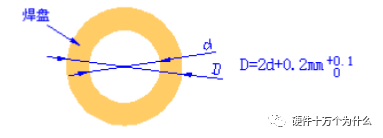
4.4.4.5針對引腳間距≤2.0mm的手插PIN、電容等,焊盤的規(guī)格為:①多層板焊盤直徑=孔徑+0.2~0.4mm;②單層板焊盤直徑=2×孔徑
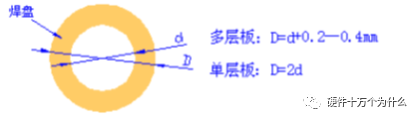
4.4.4.6 常見貼片IC焊盤設計,詳見附件(下圖只是一個選圖,相關尺寸見附件)

4.4.5 新器件的PCB 元件封裝庫應確定無誤
4.4.5.1 PCB 上尚無件封裝庫的器件,應根據器件資料建立新的元件封裝庫,并保證絲印庫存與實物相符合,特別是新建立的電磁元件、自制結構件等的元件庫是否與元件的資料(承認書、規(guī)格書、圖紙)相符合。新器件應建立能夠滿足不同工藝(回流焊、波峰焊、通孔回流焊)要求的
元件庫。
4.4.5.2 需過波峰焊的SMT 器件要求使用表面貼波峰焊盤庫
4.4.5.3 軸向器件和跳線的引腳間距的種類應盡量少,以減少器件的成型和安裝工具。
4.4.5.4 不同PIN 間距的兼容器件要有單獨的焊盤孔,特別是封裝兼容的繼電器的各兼容焊盤之間要連線。
4.4.5.5 不能用表貼器件作為手工焊的調測器件,表貼器件在手工焊接時容易受熱沖擊損壞。
4.4.5.6 除非實驗驗證沒有問題,否則不能選用和PCB 熱膨脹系數差別太大的無引腳表貼器件,
這容易引起焊盤拉脫現象。
4.4.5.7 除非實驗驗證沒有問題,否則不能選非表貼器件作為表貼器件使用。因為這樣可能需要手焊接,效率和可靠性都會很低。
4.4.5.8 多層PCB 側面局部鍍銅作為用于焊接的引腳時,必須保證每層均有銅箔相連,以增加鍍銅的附著強度,同時要有實驗驗證沒有問題,否則雙面板不能采用側面鍍銅作為焊接引腳。
4.4.6 需波峰焊加工的單板背面器件不形成陰影效應的安全距離,考慮波峰焊工藝的SMT器件距離要求如下:
1) 相同類型器件距離(如圖)
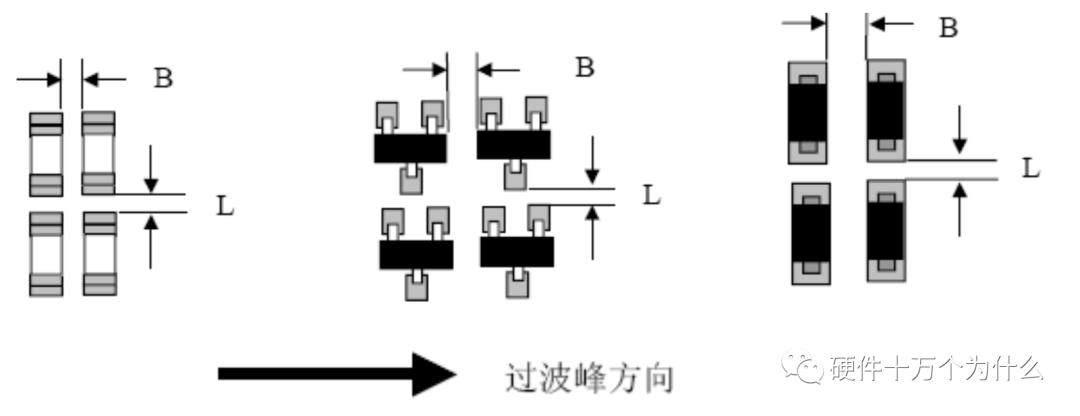
相同類型器件的封裝尺寸與距離關系:
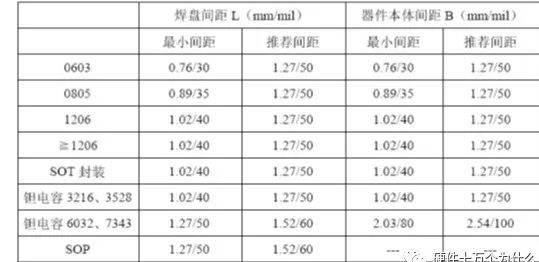
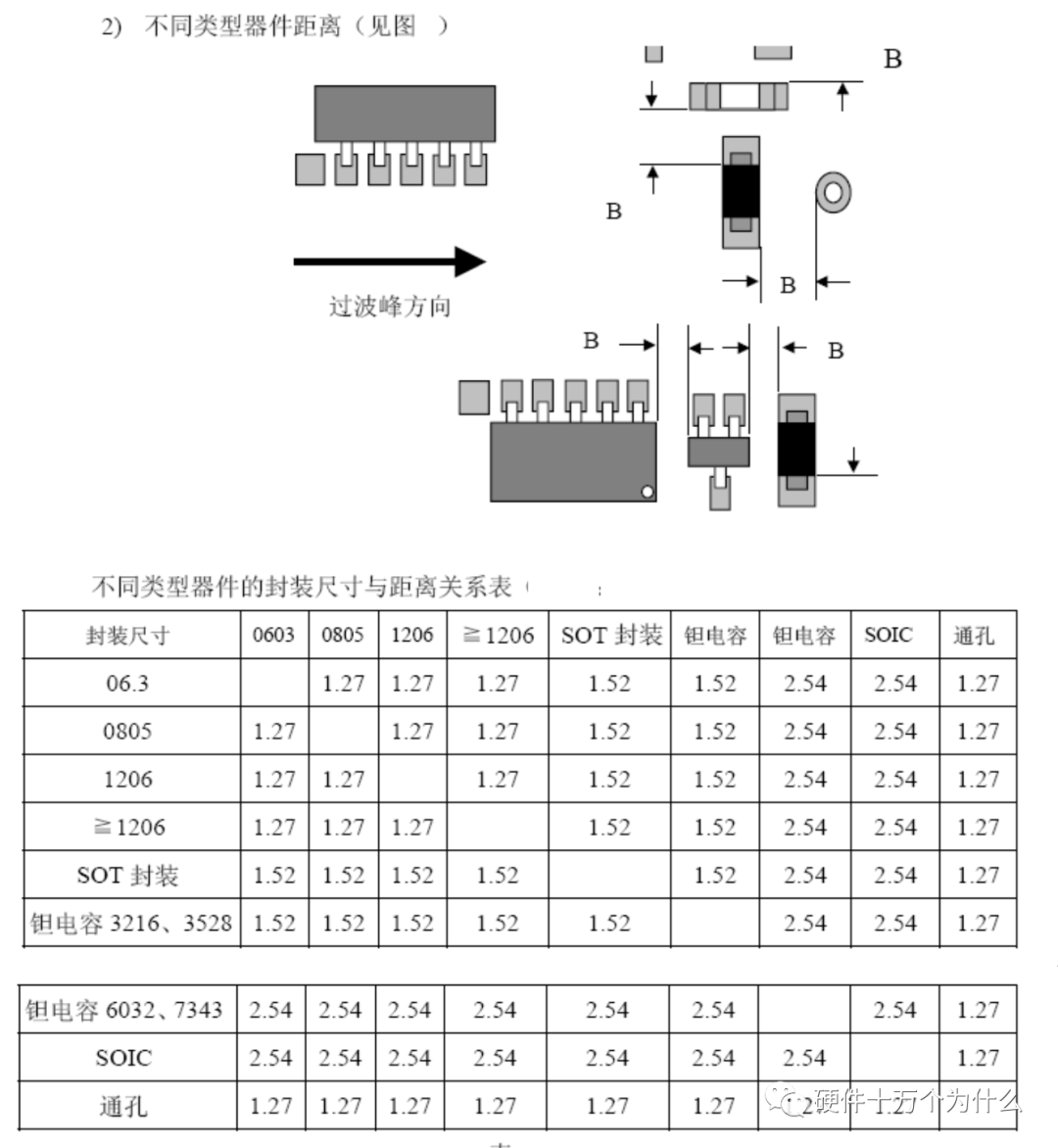
4.6.1 SMD同種元件間隔應滿足≥0.3mm,異種元件間隔≥0.13*h+0.3mm(注:h指兩種不同零件的高度差),THT元件間隔應利于操作和替換
4.6.2 貼裝元件焊盤的外側與相鄰插裝元件的外側距離大于2mm
4.6.3經常插拔器件或板邊連接器周圍3mm 范圍內盡量不布置SMD(尤其是BGA),以防止連接器插拔時產生的應力損壞器件;
4.6.4 定位孔中心到表貼器件邊緣的距離不小于5.0mm
4.6.5 大于0805 封裝的陶瓷電容,布局時盡量靠近傳送邊或受應力較小區(qū)域,其軸向盡量與
進板方向平行,盡量不使用1825 以上尺寸的陶瓷電容。(保留意見
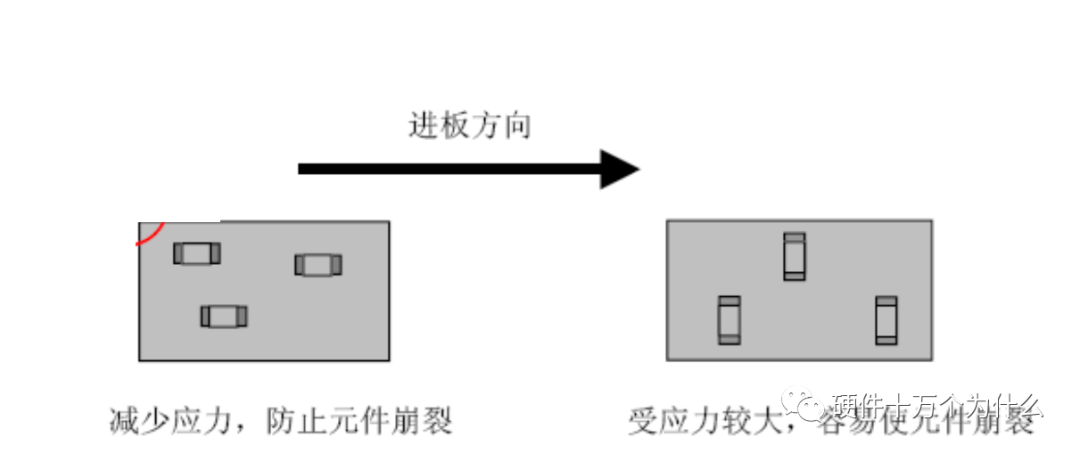
4.4.6.6 經常插拔器件或板邊連接器周圍3mm 范圍內盡量不布置SMD,以防止連接器插拔時產生的應力損壞器件。如圖:
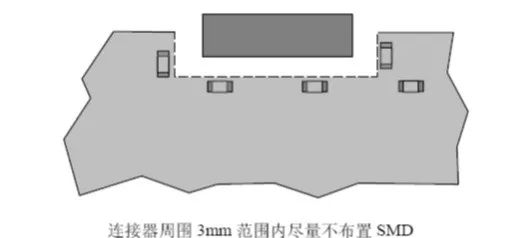
4.4.6.7 過波峰焊的表面貼器件的stand off 符合規(guī)范要求過波峰焊的表面貼器件的stand off 應小于0.15mm,否則不能布在B 面過波峰焊,若器件的stand off 在0.15mm 與0.2mm 之間,可在器件本體底下布銅箔以減少器件本體底部與PCB表面的距離。
4.4.6.8 波峰焊時背面測試點不連錫的最小安全距離已確定
為保證過波峰焊時不連錫,背面測試點邊緣之間距離應大于1.0mm。
4.4.6.9 過波峰焊的插件元件焊盤間距大于1.0mm
為保證過波峰焊時不連錫,過波峰焊的插件元件焊盤邊緣間距應大于1.0mm(包括元件本身引腳的焊盤邊緣間距)。優(yōu)選插件元件引腳間距(pitch)≧2.0mm,焊盤邊緣間距≧1.0mm。在器件本體不相互干涉的前提下,相鄰器件焊盤邊緣間距滿足圖要求
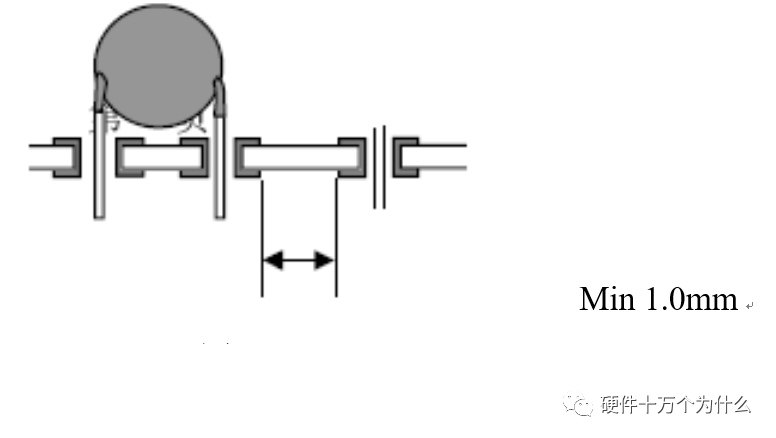
4.4.6.10 插件元件每排引腳為較多,以焊盤排列方向平行于進板方向布置器件時,當相鄰焊盤邊緣間距為0.6mm--1.0mm 時,推薦采用橢圓形焊盤或加偷錫焊盤
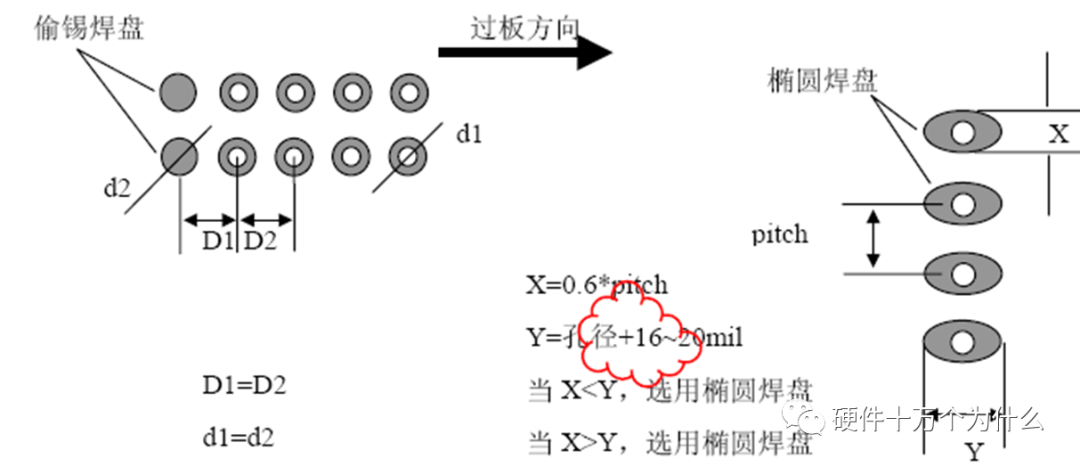
4.4.6.11 貼片元件之間的最小間距滿足要求
機器貼片之間器件距離要求(如圖):
同種器件:≧0.3mm
異種器件:≧0.13*h+0.3mm(h 為周圍近鄰元件最大高度差)
手工貼片的元件之間距離要求:≧1.5mm。
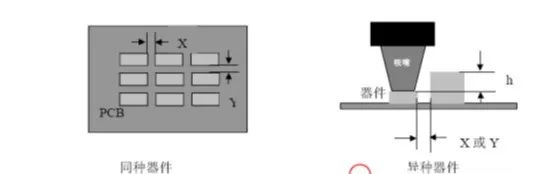
4.4.6.12 元器件的外側距過板軌道接觸的兩個板邊大于、等于5mm(圖9)
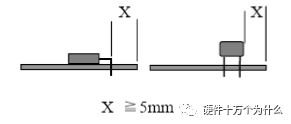
為了保證制成板過波峰焊或回流焊時,傳送軌道的卡爪不碰到元件,元器件的外側距板邊距離應大于或等于5mm,若達不到要求,則PCB 應加工藝邊,器件與V—CUT 的距離≧1mm
4.4.6.13 可調器件、可插拔器件周圍留有足夠的空間供調試和維修應根據系統(tǒng)或模塊的PCBA安裝布局以及可調器件的調測方式來綜合考慮可調器件的排布方向、調測空間;可插拔器件周圍空間預留應根據鄰近器件的高度決定。
4.4.6.14 所有的插裝磁性元件一定要有堅固的底座,禁止使用無底座插裝電感
4.4.6.15 有極性的變壓器的引腳盡量不要設計成對稱形式;有空腳不接電路時,注意加上焊盤,以增加焊接牢固性
4.4.6.16 安裝孔的禁布區(qū)內無元器件和走線(不包括安裝孔自身的走線和銅箔)
4.4.6.17 金屬殼體器件和金屬件與其它器件的距離滿足安規(guī)要求
金屬殼體器件和金屬件的排布應在空間上保證與其它器件的距離滿足安規(guī)要求。
4.4.6.18 對于采用通孔回流焊器件布局的要求
a. 對于非傳送邊尺寸大于300mm 的PCB,較重的器件盡量不要布置在PCB 的中間,
以減輕由于插裝器件的重量在焊接過程對PCB 變形的影響,以及插裝過程對板上已
經貼放的器件的影響。
b. 為方便插裝,器件推薦布置在靠近插裝操作側的位置。
c. 尺寸較長的器件(如內存條插座等)長度方向推薦與傳送方向一致。多個引腳在同一直線上的器件,連接器、DIP 封裝器件、T220 封裝器件,布局時應使其軸線和波峰焊方向平行。
較輕的器件如二級管和1/4W 電阻等,布局時應使其軸線和波峰焊方向垂直。這樣能防止過波峰焊時因一端先焊接凝固而使器件產生浮高現象;直插元件應避免使用方形焊盤(方形焊盤容易導致上錫不良和連焊)
5.相關管理內容
5.1 元件焊盤的封裝庫
5.2 PCB焊盤設計的工藝性在遵守上面規(guī)則的前提下,需要具體的變化以實際設計需要為準。
- 上一篇:一文帶你了解PCB環(huán)形圈
- 下一篇:開關電源模塊的阻抗你真的了解嗎?